Our vision is TO BE THE BEST-TASTING, SUSTAINABLE NR. 1 KIDS’ DRINK IN THE WORLD
CREATING A BETTER WORLD FOR ALL
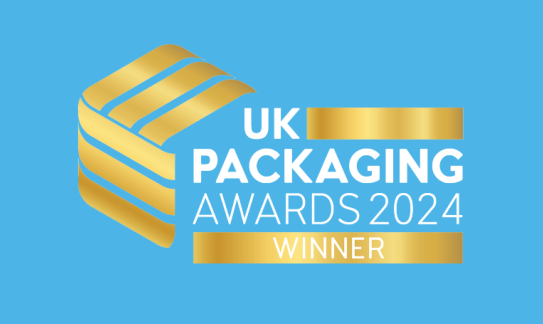
CAPRI-SUN wins Best Flexible Packaging award
This achievement at the UK Packaging Awards 2024 highlights our commitment to sustainability, innovation, and delivering the best product for our consumers. The flexible packaging solution is not only designed to keep our drinks fresh but also aligns with our goals to reduce environmental impact.
One judge said: “(...) A lighter and fully recyclable pack, offers the consumer the same convenience with no reduction in performance and offers emission and waste reduction benefits. A worthy winner.”

Why we’re proud
of our iconic pouch
- The European Space Agency developed it for use by astronauts on the International Space Station.
- Its unique design and quality production process allows us to create drinks without preservatives or artificial flavours and colours.
- Its lightweight design makes it environmentally friendly to transport.
How we recycle your Capri-Sun

See OPRL Logos on how to recycle packaging on our cartons.